Differences between pottery and ceramics:
Pottery and ceramics have been associated with human culture for thousands of years and contain most of the archaeological discoveries. Not only in the historical background of Iranians but also in religious insight and traditional medicine, much emphasis has been placed on the use of these dishes in cooking and so on. In contemporary life, the role of these dishes around us is quite noticeable, whether in functional products or in decorative structures.
The question that often arises is what is the difference between pottery and ceramics, especially in utensils?
The answer to this question is not so complicated. Ceramics are more common than pottery. Pottery products are made from clay and are made by hand with a potter's wheel, but ceramic or slurry products are made from a combination of clay and several other types of soil and materials.
Pottery or earthenware is made of clay and secondary soils that have high adhesion and a lower degree of firing. While ceramic dishes refer to bodies that are with primary soils such as a combination of kaolin, quartz, silica and stoneware soil and have less adhesion to secondary soils and require a higher degree of firing more than 1080 ° C and also have a higher glaze than pottery. Is.
Pottery and ceramic products are either glazed or unglazed. Paint and glaze is in fact the shiny and transparent coating on pottery and ceramics, which in addition to beauty increases the strength and durability of dishes. The type of paint and glaze depends on the type of formula and its ingredients. Therefore, by combining the ingredients of the glaze in different amounts, a new paint and glaze can be invented. The most important types of glazes are lead glaze, ash glaze and feldspar glaze.
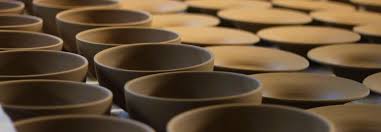
What distinguishes the color and glaze of ceramics and pottery is the transparency and colorability, which in pottery due to the red color of iron in clay causes darker colors and maturity. For example, the turquoise color on the pottery bed is slightly darker due to the red pigment, but on the ceramic bed it is clearer and without redness. For this reason, the number of paints used on ceramic dishes is much more than pottery.
To glaze pottery and ceramic dishes, they must be heated to a certain temperature. If the temperature is too high, the glaze will burn. For this reason, in order to perform the glazing steps correctly, the container must be placed in a suitable temperature range.